Test and Tag Perth
Professional testing and tagging services to protect your business against fires caused by electrical failure or malfunction!
- Fully qualified and always positive experienced technicians
- Able to complete any test and tag job, no matter how big or small
- Efficiency testing by utilising the latest in test equipment
- 24/7 available for your safety
- Durable printed test tags
How our test and tag service in Perth works
What is Test and Tag?
Ensuring the safety of electrical equipment according to the Australian Standard is commonly referred to as testing and tagging.
Here at Fantastic Services, we have a wealth of experience in helping businesses meet compliance obligations, as required by WHS legislation. The competent people can help you comply with Australian Standard AS/NZS 3760, which outlines the testing and tagging procedures that may be required.
The complete electrical testing process involves inspecting, electrically testing (with a Portable Appliance Tester, also known as PAT tester) and then labeling and logging the results of the electrical tests. Testing and tagging to the Australian Standard AS/NZS 3760:2010 helps to ensure electrical safety in the workplace and can dramatically reduce the risks of electrocution and fires.
Electrical safety testing should be a routine part of how a Person Conducting Business or Undertaking (PBCU) handles the maintenance of all fitting and appliances in the workplace. However, it is not legally mandatory to do so.
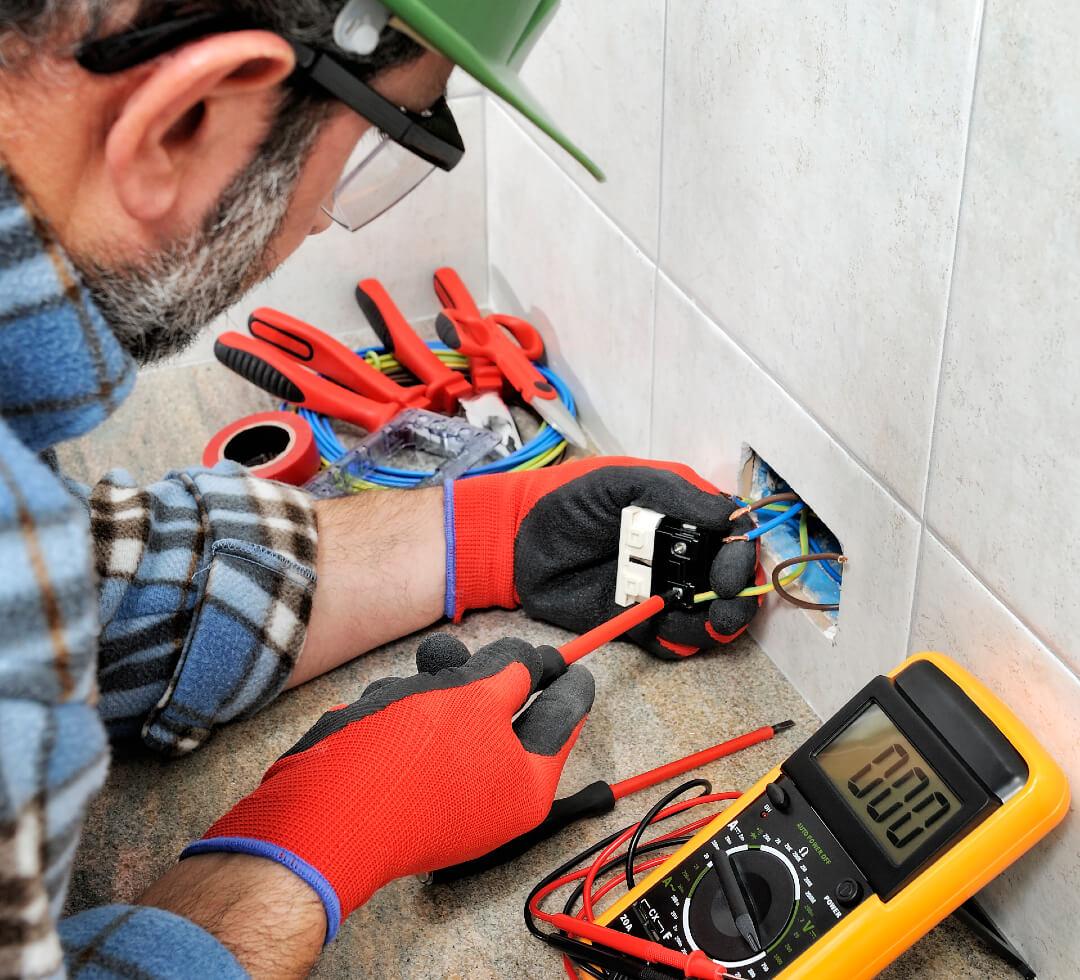
How often should testing and tagging be done?
Testing and labeling electrical equipment and portable appliances for a company in Australia is an important task that must be done systematically, no matter which industry they belong to. Getting their appliances tested and tagged after every few months is an effective way to ensure a safe working environment for all employees at all times.
Every workplace is different and has its own test & tag requirements, therefore the Australian workplace safety standards outline the intervals at which testing and tagging of appliances must be carried out in each industry.
- Every 3 months - Demolition, construction and building industry
- Every 6 months - Production, warehouses and factories
- At least once a year - Hostile environments
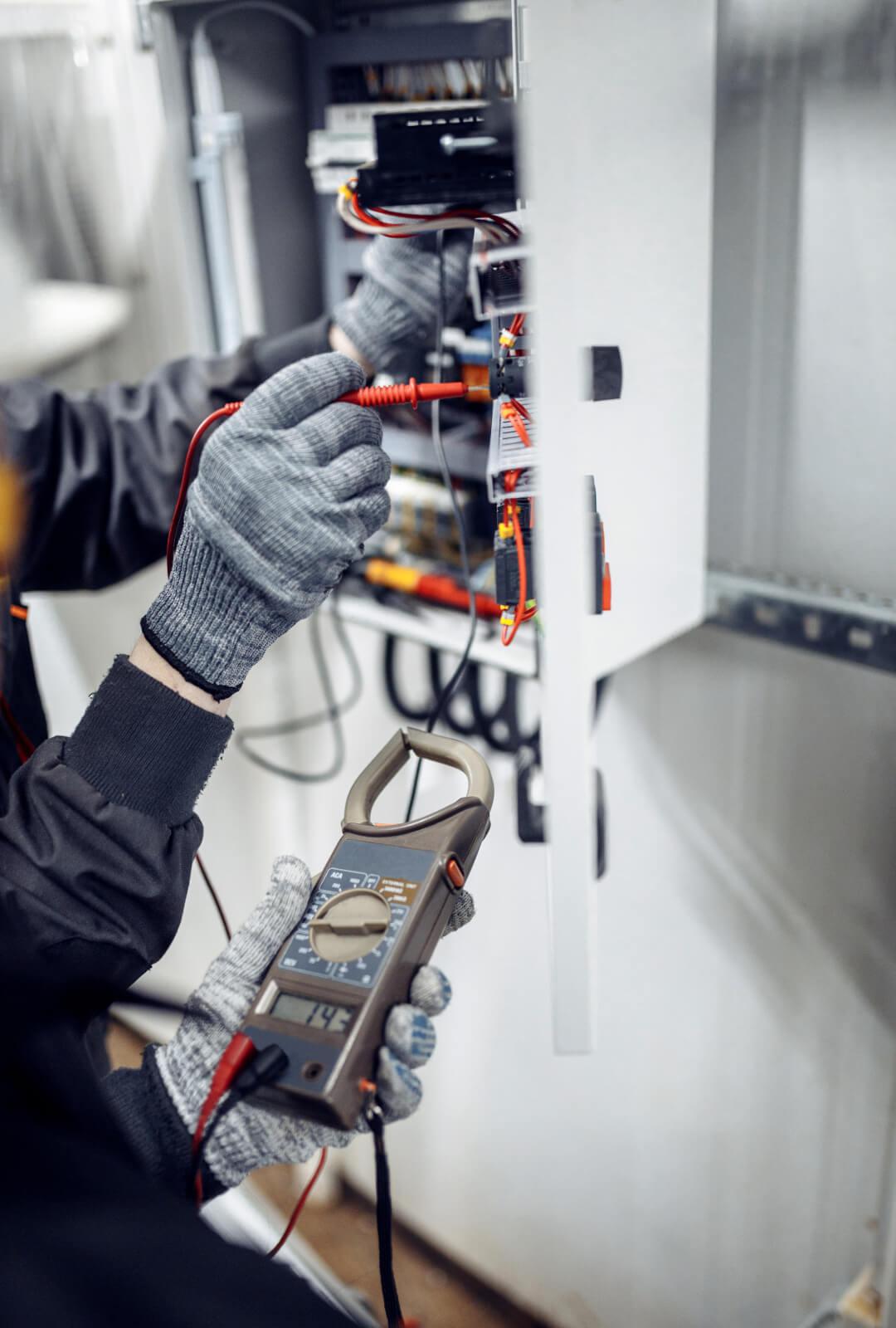
Why choose Fantastic Services in Perth for test and tag job
Our test and tag experts are part of the local community and have been serving customers in Perth for over 10 years. All of our teams are highly qualified and professional, and have years of experience with domestic and commercial electrical work. We are proud to say that our passion and experience within the industry has helped us win large clients all around Perth.
Our Test and Tag Process Explained
Here is the process when your Perth test and tag technician arrives:
- Starting with a visual inspection of the appliances.
- The next step is to perform electrical testing.
- Tagging (including correct color coding for construction, mining, and demolition), which includes your next service due date.
- Issuing a full report, including passes and fail, location & description of the appliance.
- Providing the customer with a Certificate of Compliance.
- Creating a note in our system to contact you when your next testing and tagging service is due, so you don’t need to worry about chasing us up.
The specialists will conduct the following processes and inspections as required.
External Inspection of equipment. Checking for damage, defects, wear or modifications to the equipment. Checking the plugs / connectors for discolouration and wear; a possible sign of excessive heat, loose electrical connection, chemical or moisture exposure.
Protective Earth Continuity Test. Ensuring the resistance is sufficiently low to ensure correct operation of the equipment.
Insulation Test. Testing the leakage current insulation resistance of the device.
Polarity. Ensuring correct wiring has been completed of the equipment, It is not uncommon to see the neutral and live conductors reversed.